Our petroleum-based transportation system has led to health and climate impacts felt throughout the world. Electrifying transportation is a valuable tool we can use to reduce those impacts. This transition will require an increase of minerals used in batteries that power our electric vehicles (EVs), trucks, and buses.
When these electric transportation modes retire, the batteries’ usefulness continues. Even with diminished capacity, they can be reused, refurbished, or repurposed and then eventually recycled. The materials recovered from recycling can be used to manufacture new batteries, therefore reducing the amount of newly mined materials necessary to meet upcoming mineral demand.
The EV battery recycling business is just now kicking off, and because of the high value materials in lithium-ion batteries, the economics of this early industry look good. Batteries are being recycled, which has led some to make the case that there is no need for a strict recycling policy because the market will take care of itself. However, the positive economics of battery recycling may not last forever, nor will there be a nickel (get it?) to be made from every EV battery.
Recycling may not always be profitable for lithium-ion batteries that don’t contain cobalt and nickel, batteries that are damaged, or for small volumes of batteries located in remote locations. Considering there is no recycling requirement for retired EV batteries in the US, when the cost of recycling or repurposing a battery is greater than the profit generated, there is risk that the batteries will be landfilled or mishandled.
To avoid this very real possibility, we need an extended producer responsibility recycling requirement. This means being clear about who is on the hook for unprofitable or otherwise unwanted EV batteries. The California legislature is beginning to take on EV battery recycling with Senate Bill 615 which is currently in initial draft form. So, we’ve decided now would be a good time to explain the problem and the need for a fool-proof solution.
While EVs retiring today are a trickle, this will increase exponentially
The number of batteries retiring today is relatively small in comparison to the number of batteries that will be retiring in the future. This is because EVs have only been a small fraction of auto sales over the last decade. As California transitions to 100% zero emission vehicle sales by 2035, there will be more EVs on the road and batteries eventually ready for recycling.
As the number of retiring batteries increases there is the potential for more batteries to slip through the cracks and not be recycled. An extended producer responsibility can help ensure high recycling rates with the safe and high recovery of materials.
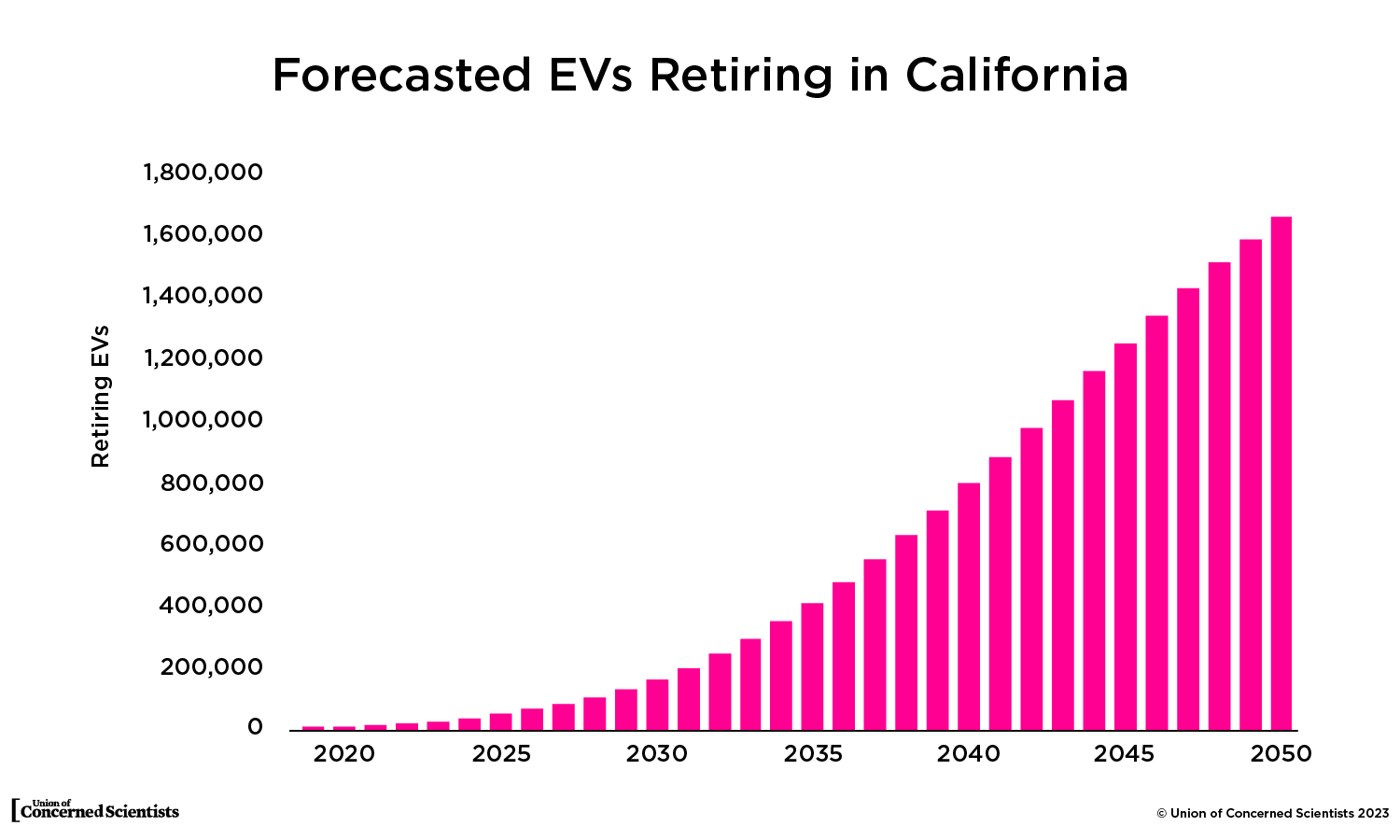
Yes, EV batteries can be recycled
Batteries can be recycled and there are companies doing so in North America. One US based recycling company has reported that they will take all batteries, even if they are not profitable to recycle. This is part of their research to identify where batteries are retiring and design efficient collection routes.
Once there is a larger availability of batteries from retiring EVs, recyclers can be a bit pickier as to the batteries they collect. They will likely make the strategic decision to choose those with positive economics, like the batteries that contain cobalt and nickel. Unfortunately, batteries like lithium-ion-phosphate (LFP) that don’t contain these two valuable materials currently represent a cost to recycle. Since LFP is only a fraction of retiring supply, it doesn’t seem to be a problem yet, but their market share is increasing. As more EVs retire, and as technology changes, recycling companies will likely prioritize batteries of higher material value, better health, and a shorter distance to travel.
Since it can’t be guaranteed that recycling all EV batteries will be profitable, it is essential that we ensure a future where even these get recycled and handled safely to avoid improper disposal or them wasting away in landfills.
Instances where there is a disincentive to recycle
Scenario 1: Higher than average cost to collect and transport.
The costs associated with recycling includes the collection and transportation of the battery (about 29%), the dismantling and disassembly (about 37%), and then the recycling process (about 34%). The collection and transportation costs vary based on whether the battery is damaged, the distance to a recycling facility, and the volume of batteries shipped.
Damaged batteries have an increased risk of fire and as a result require extra precautions to ship. This includes additional packaging that must be custom made and comply with the United Nations standards.
Shipping costs per battery also increase with longer distances to travel and when only a few batteries need to be transported. This typically occurs when they are located in remote areas and there aren’t enough to fill a truck. In this scenario, the truck with the special Class 9 hazardous permit is transporting only a couple batteries, therefore operating at partial capacity.
These shipping costs can be decreased with an efficiently designed collection network that optimizes collection points and the infrastructure already in place, such as the currently operating dismantlers and dealerships. Manufacturers are in the prime position to do this centralized planning to ensure that operations are in place for all batteries to be recycled and reap benefits from economies of scale.
Scenario 2: The LFP lithium-ion battery has low revenue from material recovery.
Revenue from selling the minerals that can be recovered from the battery make up the profit from recycling. Batteries that are currently retiring have high amounts of cobalt and nickel, two very valuable minerals. These minerals have been instrumental in EVs success, allowing batteries to be smaller while enabling EVs to go further. There are some alternatives, including lithium-iron phosphate (LFP), that do not contain either of these minerals. LFP hasn’t historically been used in EVs sold in the US because the batteries have to be bigger than the nickel and cobalt alternatives to provide the same amount of energy. This is changing as technology develops and EVs become more prevalent.
Tesla has begun producing a lower range and less expensive EV that uses an LFP battery. Ford, Rivian, and Volkswagen also have plans for using LFP. Since these batteries contain lower value materials, they are also less valuable to recycle. My research and others evaluating recycling economics finds that recycling LFP is not currently profitable, therefore creating a disincentive to eventual recycling that may lead to low recovery rates.
Manufacturers can reduce the costs associated with recycling. Extended producer responsibility would incentivize designing these batteries to be more safely and efficiently disassembled which would result in decreased costs of recycling. As mentioned above, the dismantling and disassembling of the battery is estimated to represent about 37% of recycling costs. This is a substantial portion that varies by manufacturer and model because it is based on the time it takes for people to complete the process by hand. The process is lengthy because the battery is not designed to be disassembled and due to lack of standardization, the batteries cannot be taken apart by robotics.
Decreasing the cost of recycling through designing for disassembly has the potential to drive the recycling cost of LFP batteries down, which contain a valuable source of lithium. Recycling technologies in development could also lead to profitable recycling of LFP, therefore representing another potential area of investment for manufacturers that would be incentivized to make LFP recycling profitable.
All EV batteries need to be recycled
A strong recycling policy is essential to ensure that all EV batteries are safely recycled so that the materials can be recovered. If recycling requirements are not enacted, there is the possibility of batteries not being recycled if it is not profitable to do so. This could be either due to the batteries being damaged, in a remote locations, or of lower mineral value.
In addition, if the responsibility of recycling is placed on automotive dismantlers, there is the possibility that these batteries with a disincentive to recycle are pushed into the unlicensed and unregulated dismantling market. This market processes approximately 30% of retiring cars in the US and presents a large environmental and safety risk.
We suggest that an extended producer responsibility program with a recycling requirement is enacted to ensure all batteries are recycled and to drive recycling costs down. This is essential for reducing the amount of mining needed to electrify our transportation system over the next several decades. This policy is an important aspect in meeting our long-term goals of creating a low impact and circular transportation system.